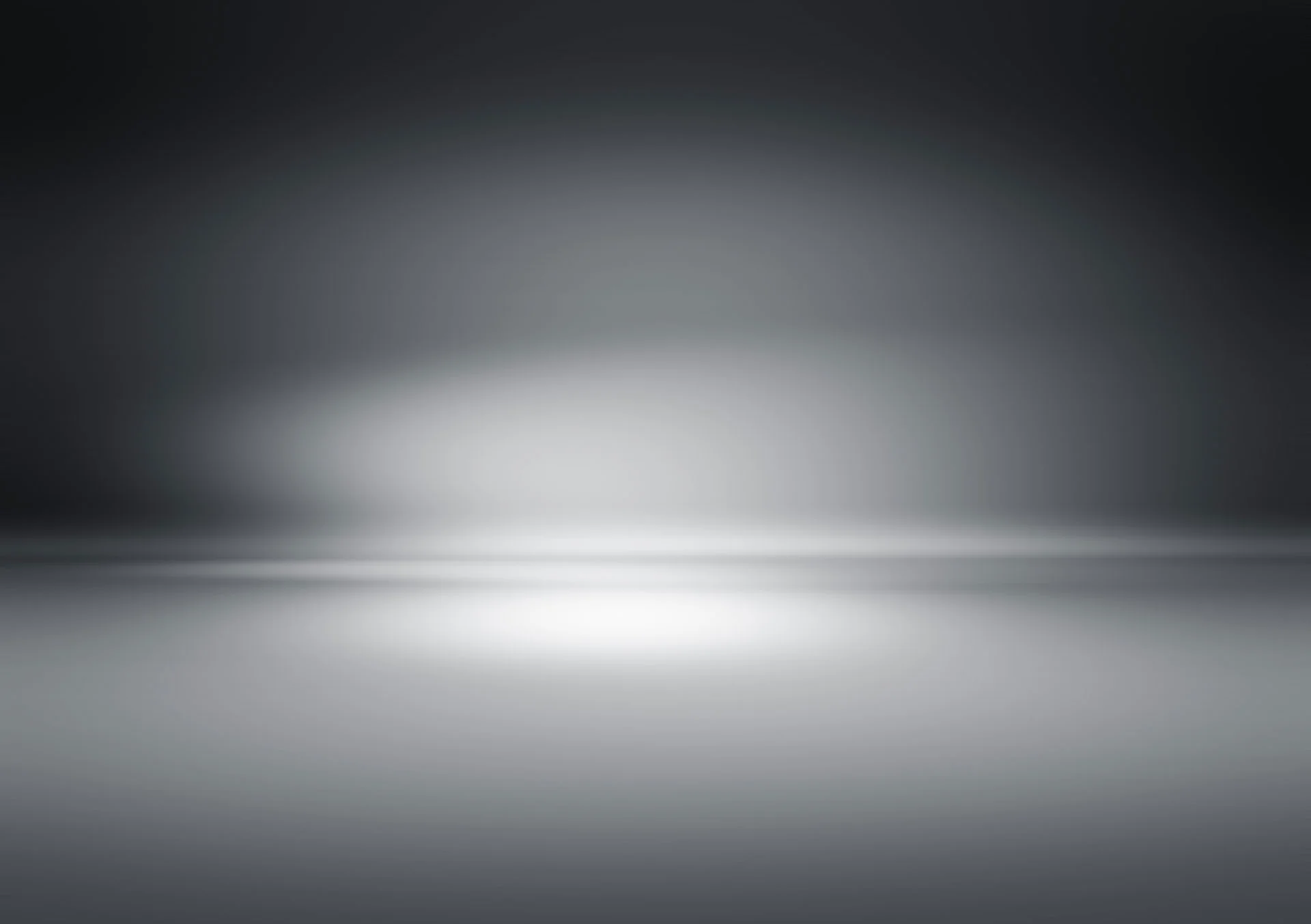
The conversions of these cars was more than just replacing and bolting a few panels on a stock C5 or C6 Corvette.
Every exterior panel on the original Corvette was replaced with a computer engineered Carbon Fiber panel. The conversion was designed to use factory stock parts (hinges, wiring, interior appointments). The bumpers and most of the chrome trim were manufactured specifically for CRCoachworks, or by CRCoachworks, with some of them being chromed carbon fiber.
Each car was hand crafted and took over 900 hours to complete. Panels and trim were custom fit and the car was painted the color selected by the customer.